Water Borehole at Müller’s Production Facility
Igne was commissioned to drill a 90-meter borehole with a diameter of 17.5 inches at Müller’s production facility in Market Drayton. This new borehole was intended to serve as a backup for an existing one on site, which had deteriorated and had its pump stuck. The goal was to ensure the facility could maintain operations while addressing the issues with the current borehole.
Project Challenges
- Proximity issues: the new borehole had to be drilled close to the existing one, necessitating the shutdown of the production well during drilling to prevent cuttings from being drawn in.
- Operational risks: shutting down the production well posed a risk of the pump not coming back online, requiring contingency planning.
- Logistical coordination: work had to be planned around the facility’s maintenance shutdowns, necessitating precise scheduling and preparation.
Project Execution
Igne proposed a phased work plan to minimise risks, suggesting that work would be carried out across two shutdown periods. The planning process began in September 2023, with meticulous preparation and coordination to ensure minimal disruption to the production facility.
A detailed programme of works was developed, focusing on cautious progression.
Brand new drilling bits and a mud treatment plan were employed to optimise drilling efficiency.
Direct flush with high-pressure jetting pumps was used instead of reverse circulation, significantly increasing penetration rates.
The team prepared for potential equipment failures and overcame the lack of water on site by having four 25 cubic metre tankers for water and a turnaround system for delivering clean potable water.
All hire plant was doubled up to allow immediate replacement if needed, and a fitter was retained on call to ensure any mechanical issues could be resolved within a guaranteed four-hour window.
Igne’s owned plant was serviced and tested before deployment to the site, and there was a comprehensive briefing and induction for all team members to ensure readiness from the moment of arrival.
Despite initial plans for two shutdown periods, the team managed to complete the drilling to the required 90 meters in one go. The plastic liner and filter pack were successfully installed in a single attempt as well.
This efficiency saved Müller a significant amount of money and minimised disruption to their operations.
The Project Outcome
The project was completed ahead of schedule and within budget, showcasing Igne’s capability to deliver under challenging conditions. The careful planning, experienced personnel, and use of advanced techniques contributed to this success.
Client Testimonial
"Just a quick email to thank you & in particular the guys on site for all the great work that took place over the last week. Personally, I feel it’s been a phenomenal achievement and as I noted this is mainly down to the team you sent here, some of the best contractors I’ve ever worked with."
This project highlights Igne’s commitment to excellence, innovation, and client satisfaction. By overcoming significant logistical and technical challenges, Igne successfully delivered a crucial infrastructure project, ensuring uninterrupted production for Müller’s facility.
Other articles of interest

Borehole renovation for a food manufacturer
This case study details a project undertaken to drill a 720mm borehole for a food processing facility to rectify issues left by a former drilling company. We successfully drilled a new borehole to pump 120m3/hr.
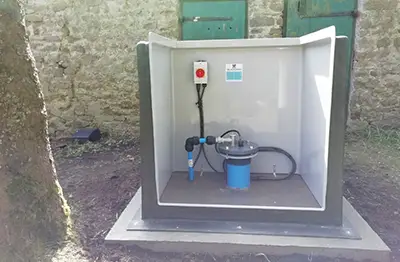
Refurbishing water boreholes
As well as drilling boreholes and inspecting and maintaining them, the teams at Igne are often called to wells that need refurbishment.